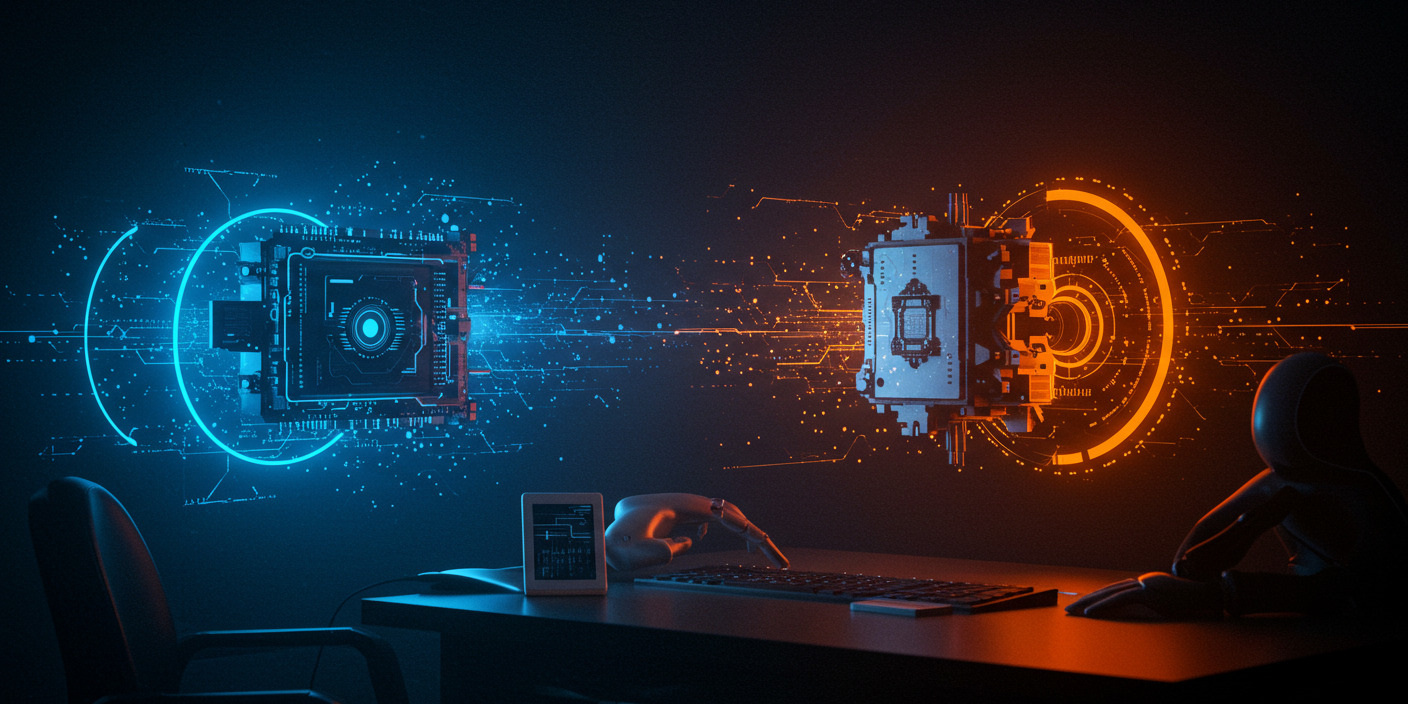
For years, “zero defects” has been the ultimate quality control goal — a kind of manufacturing utopia. The idea is simple: produce products so consistently perfect that no defects slip through. The reality? Much harder. Humans miss things. Traditional sensors have limits. And even the best-designed processes occasionally break down.
But now, something’s changed. AI-powered vision systems are entering the conversation, not as a silver bullet, but as a serious contender for closing that last quality gap. So let’s ask the big question: can AI vision actually get us to zero defects?
Why Zero Defects Has Always Been Hard
Before we jump to solutions, it’s worth understanding the challenge.
Here’s what stands in the way:
-
Human fatigue: Even the best inspectors get tired or distracted after hundreds of parts.
-
Tiny variations: Hairline cracks, subtle discolorations, or microscopic surface defects are easy to miss.
-
High throughput: Modern production lines move fast — faster than any human eye can track consistently.
-
Subjectivity: What one inspector sees as a flaw, another might pass as acceptable.
These problems don’t just waste money. They can damage customer trust and trigger expensive recalls. That’s why manufacturers across industries — from automotive to electronics to packaging — are exploring whether AI vision can take them that final step.
How AI Vision Works in Defect Detection
Let’s demystify this.
AI vision systems combine high-resolution cameras and machine learning algorithms to analyze images of products at various production stages.
Here’s the basic workflow:
-
Image capture: Cameras or sensors take rapid-fire pictures of products in real time.
-
Preprocessing: Images are cleaned up (noise reduction, contrast adjustments) to prepare for analysis.
-
Feature extraction: Algorithms scan for patterns that match known defect types — or even anomalies never seen before.
-
Decision-making: The system classifies the product as pass/fail or flags it for further inspection.
The real magic? AI systems can be trained to recognize both obvious flaws and tiny inconsistencies that humans might miss, all at line speed.
The Big Gains We’re Seeing
So far, the companies that have taken the leap aren’t disappointed.
Increased Detection Accuracy
AI models don’t get bored or distracted. They spot surface defects, dimensional inaccuracies, or coating inconsistencies with remarkable consistency.
Faster Feedback Loops
Real-time alerts mean defects get caught immediately, not downstream during final audits or, worse, after shipping.
Cost Savings
Catching defects early reduces waste, scrap, and costly rework. It also minimizes the chance of customer returns or warranty claims.
Scalability
Once trained, AI systems can run 24⁄7 without breaks and be rolled out to multiple lines or plants with relatively minor adjustments.
Can It Really Eliminate All Defects?
Here’s where it gets interesting — and where we should be honest.
What AI Vision Does Well:
-
Detects repeatable, surface-level defects with high precision.
-
Flags unexpected anomalies that humans may never have noticed.
-
Works well on high-volume, consistent production lines.
Where It Struggles:
-
Complex assemblies: When defects are hidden deep inside a product, cameras can only do so much.
-
Unstructured environments: Environments with lots of random variation (think food processing) are harder to model.
-
Edge cases: Extremely rare defects that haven’t been seen before can sometimes confuse the model.
In short, AI vision dramatically reduces defects but isn’t infallible. It’s best used as part of a hybrid system: AI handles the repetitive bulk, and skilled human inspectors step in for exceptions and judgment calls.
Lessons from Early Adopters
The companies closest to “zero defects” with AI vision share a few common strategies:
1. Start Small, Then Scale
They don’t try to automate the whole process at once. They pick a high-defect or high-cost area and pilot there first.
2. Keep Humans in the Loop
Successful deployments use AI to augment — not replace — the human workforce. People handle exceptions and verify borderline calls.
3. Treat It as Continuous Improvement
Models improve over time. The more data you give them, the smarter they get. Companies that embrace iteration see the best long-term results.
4. Don’t Forget the Basics
Even the best AI system fails if cameras are poorly positioned, lighting is inconsistent, or maintenance is sloppy.
So… Can AI Vision Get Us to Zero Defects?
The honest answer? Almost.
AI vision won’t magically make defect risk disappear. But it will take you a lot closer than any human-only system ever could. For many industries, it already means defect rates so low that they’re no longer a business risk.
The companies leaning in now — testing, learning, tweaking — are the ones building a quality edge their competitors will scramble to match later.
If you’ve got a process where defects are eating time and profit, it might be time to ask: what would it look like if AI helped? Not in theory. Right now.
That’s where the real road to zero defects starts.